Revolutionizing the Workplace: Navigating Industry 4.0 for Employers
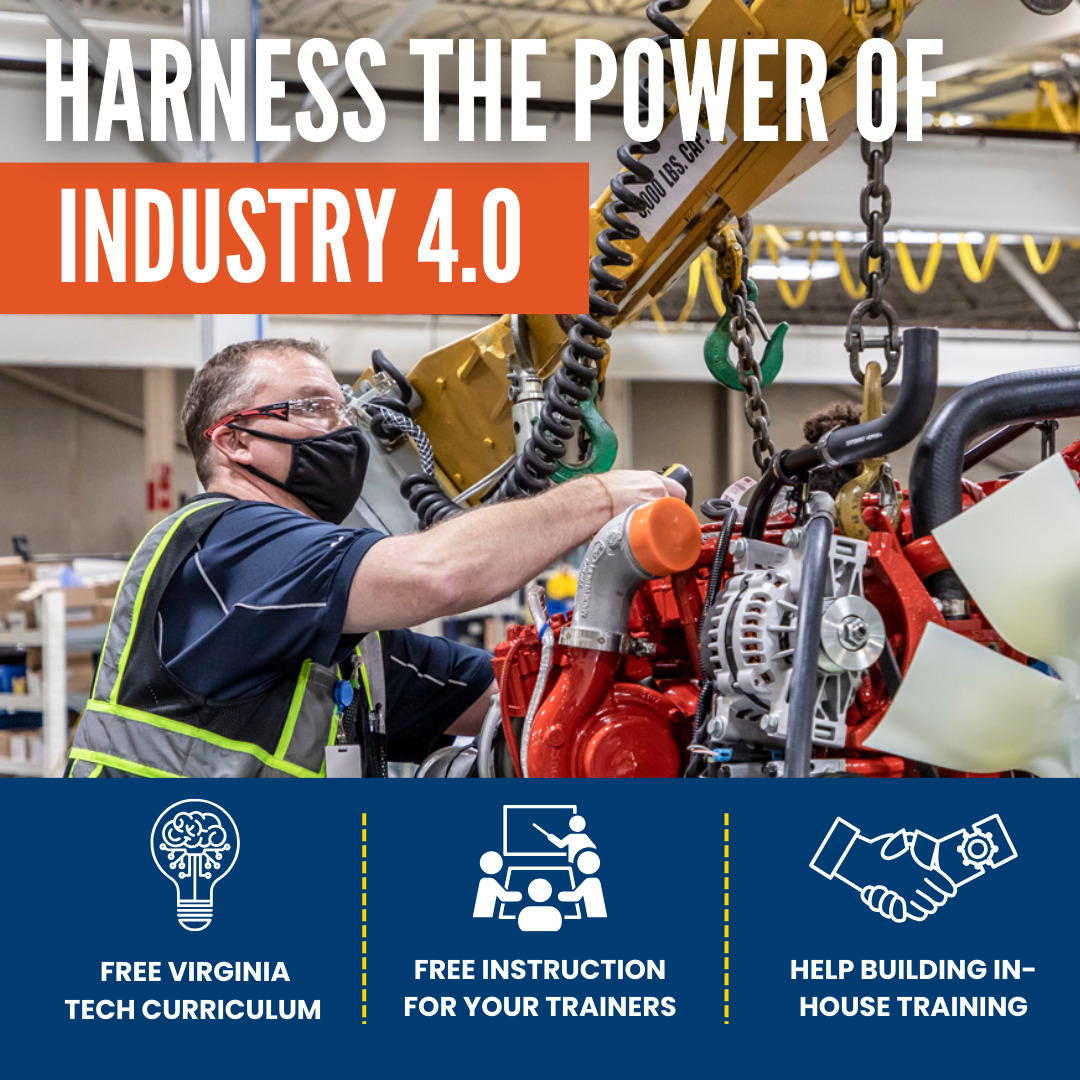
Harnessing the Technology of the Fourth Industrial Revolution
Each time transformational technology has been added to the landscape of business and manufacturing, there has been an industrial revolution (think gas-powered machines, electronics, nuclear power, and the internet). The fourth industrial revolution is here (some might argue the fifth is upon us), and industries across the world are harnessing the power of cutting-edge technologies such as additive manufacturing, Internet of Things (IoT), robotics, artificial intelligence, autonomy, automation, and more.
Changing your entire company structure to marry new technologies with old systems can feel overwhelming and requires cooperation from the C-suite down to trainees. Thanks to a project led by GO Virginia and Virginia Tech College of Engineering, the Roanoke Region of Virginia now has access to free Industry 4.0 curriculum, training, and implementation-plan development. Get your entire company thinking with future tech in mind.
Contact the program coordinator to learn more about the training and curriculum, or join one of the upcoming information sessions or workshops.
Benefits of Implementing Industry 4.0
Industry 4.0 technologies extend their influence across various sectors, including manufacturing, transportation, retail, agriculture, healthcare, banking, emergency response, and education. To thrive in the rapidly evolving digital economy, introducing your workforce to the knowledge of Industry 4.0 becomes imperative. Industry 4.0 planning and training can affect your company’s bottom line in a variety of ways, but below are a few positive outcomes Industry 4.0 practitioners can point to:
- Increasing labor productivity, production capacity, and reducing material losses
- Improving customer service, delivery lead times, and supply chain efficiency
- Leveraging digitized operational data for business decision making
- Facilitating more effective human-computer-robot production environments
- Achieving higher employee satisfaction from being part of the transformation process
- Capitalizing on existing talent and improving skill sets to elevate the intrinsic value of your workforce
- Reducing environmental impact through waste reduction, water consumption, and energy efficiency
Source: McKinsey & Company
“The recent pandemic underscored the need for resilient manufacturing capabilities. The increased demand for growth and the constraints of traditional workforce development put manufacturers in a bind. Industry 4.0 presents an opportunity for manufacturers, especially small ones, to adopt advanced technologies, enhance productivity, and provide upskilling opportunities for sustainable growth.“
–Dean Young, Vice President, Business Transformation, GENEDGE Alliance
Prioritizing Industry 4.0 in the C-Suite
If you’re serious about your Industry 4.0 future, it must be initiated in the C-suite first. Without that level of engagement, real change is next to impossible, and you could find yourself outpaced by competitors.
To build your Industry 4.0 plan for success, identify a leader with the experience to:
- Analyze and solve gaps in your digitalization strategy.
- Identify areas where your investment will have the greatest impact on overall safety, efficiency, agility, and operational control.
- Drive cultural change and empower your workforce to embrace innovation and advocate for digitally driven solutions.
Source: Forbes.com
What Does Industry 4.0 Training Entail?
Luckily for employers in the Roanoke Region, the GO Virginia and Virginia Tech Industry 4.0 Curriculum breaks down the content into modules relevant to different experiences and education levels.
- Module 1: Overview of Industry 4.0 and the Foundation Skills Required (This could be relevant for CTE students in high school and learners being introduced to Industry 4.0 concepts by employers.)
- Module 2: Soft Skills Required in Industry 4.0 Organizations (Focuses on self-awareness and critical thinking; machinery communications and the basics of network structures, protocols, procedures, etc.)
- Module 3: Industry 4.0 Professional Education (Continued education for professionals already working within Industry 4.0. Includes advice/support developing business plans and new products.)
View upcoming trainings here.
“Given the recent demographic trend of baby boomers exiting the workforce and the challenges of recruiting Millennials and GenZ into the manufacturing sector, these ‘connected solutions’ are now becoming far more valuable in terms of creating a work culture where our next generation of leaders will thrive. Wealth creation from these technologies is also opening more pathways to the middle class for a broader segment of our communities. it is an exciting time to be involved in Industry 4.0!”
-Jay Foster, Founder and CEO
Create Higher Paying Jobs and ACE Employers
Automated-Connected-Electrified (ACE) employers will be global leaders in next-generation manufacturing and automation, and we’re here to make sure that Roanoke Region employers are those leaders. With demographic shifts in the workforce, these technologies create a work culture conducive to the growth of the next generation of leaders, fostering wealth creation and broadening pathways to the middle class. You won’t need 1000 employees to run a high-volume, productive plant anymore – you need 200 Industry 4.0 savvy employees.
Industry 4.0 is not just a technological revolution; it’s a strategic imperative for employers. Embracing these transformative technologies and investing in workforce education can position your organization at the forefront of the evolving industrial landscape. As Industry 4.0 unfolds, be the catalyst for change, unlocking the true potential of your workforce and ensuring sustained success in the digital age.